What is the multi-stage injection molding speed segmentation?
The basis for setting the multi-stage injection molding speed segmentation must consider the mold’s geometry, other flow restrictions, and instability factors.
The multi-stage injection molding speed must be set with a clear understanding of the injection molding process and material knowledge. Otherwise, the product quality will be difficult to control.
The melt flow rate is difficult to measure directly. Still, it can be indirectly deduced by measuring the screw forward multi-stage injection molding speed or cavity pressure (to ensure no leakage of the non-return valve).
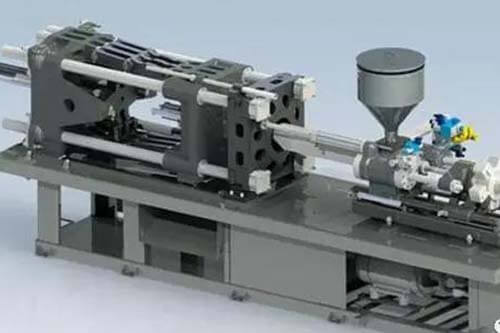
The following velocity multi-stage injection molding speed segmentation principles are recommended.
1) The velocity of the fluid surface should be constant.
2) Fast injection should be used to prevent the melt from freezing during the injection process.
3) The multi-stage injection molding speed setting should consider the fast filling in the critical area (e.g., flow channel) while slowing down the speed at the inlet level.
4) The multi-stage injection molding speed should ensure the cavity is filled and stopped immediately to prevent overfilling flying edges and residual stresses.
Material properties are very important because the polymer may degrade due to different stresses, and increasing the molding temperature may lead to intense oxidation and degradation of the chemical structure.
At the same time, the degradation caused by shear becomes less because the high temperature reduces the viscosity of the material and decreases the shear stress. Undoubtedly, multi-stage injection speeds are useful for molding heat-sensitive materials such as PC, POM, and UPVC and their compounding.
The geometry of the mold is also a determining factor: thin-walled parts require maximum injection speed.
Thick-walled parts require slow, fast, and slow profile multi-stage injection molding speed profiles to avoid defects.
To ensure that the part quality is up to standard, the multi-stage injection molding speed should be set so that the melt front flow rate is constant.
The melt flow rate is very important because it affects the part’s molecular alignment direction and surface condition.
The melt front should be slowed down when it reaches the cross-area structure.
A proportional increase in melt throughput should be ensured for complex molds with radial diffusion.
Long runners must be filled quickly to reduce cooling of the melt front, except injecting high-viscosity materials, such as PC, where too fast a speed can bring cold material into the cavity through the inlet.
Adjusting the multi-stage injection molding speed can help eliminate defects caused by slowing flow at the inlet level.
When the melt passes through the nozzle and runner to the inlet, the surface of the melt front may have cooled and solidified, or the melt may stagnate due to the sudden narrowing of the runner until enough pressure is built up to push the melt through the inlet, which causes the pressure through the inlet to appear.
Besides the Multi-stage Injection Molding Speed Segmentation Principles article, you may also be interested in the below.