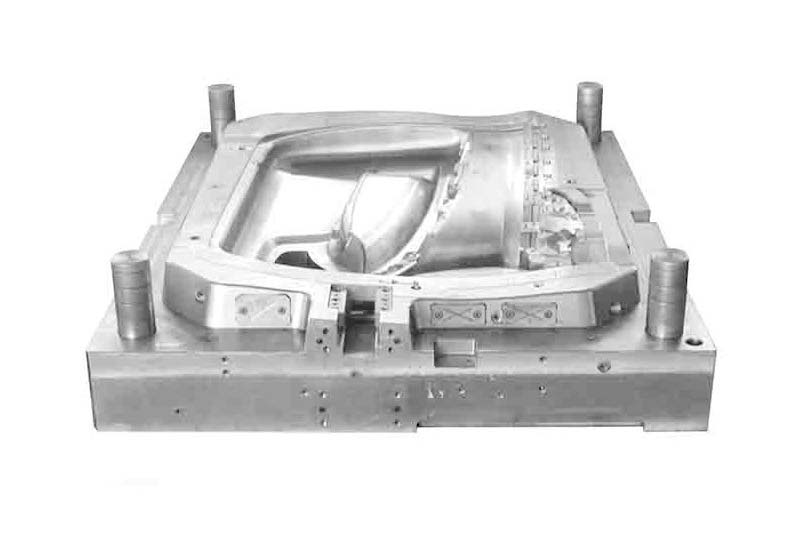
After reading this 5 Special Precision Injection Moulding Design Guides article, you will know 5 important points of precision injection moulding design guidelines.
Injection moulding is one of the most important plastic moulding methods. How to improve the level of injection moulding technology, produce high-precision plastic products and create high value-added products, the design of mould is a very important link.
In the injection moulding mould design, in addition to the basic precision injection moulding design guides should be considered, but also the below 5 special precision injection moulding design guidelines consideration of the following matters.
Special Precision Injection Moulding Design Guide 1. Appropriate mould dimensions and tolerances
1. The relationship between product size accuracy and mould size accuracy
Draw the product map and consider the mould design, making, and forming process. First of all, from the product map size mould map size. Make the mould according to the size of this mould drawing, and get the actual size.
Using this mould, we can obtain the moulded product and get the actual size of the product. The question is how to ensure that the actual size is within the dimensional tolerances required by the design of the drawing.
2. Appropriate shrinkage rate
In the process of moulding products, even if the same resin with the same pigment is used, the shrinkage rate varies according to the different moulding conditions. In precision moulding, the degree of change in shrinkage should be small, and there should be no difference between the expected shrinkage and the actual shrinkage as much as possible.
Shrinkage is mainly assumed by combining the actual shrinkage of similar products in the past. Actual shrinkage is also assumed by using an experimental mould, and then correcting and designing the mould for actual production.
However, it is almost impossible to determine the shrinkage rate appropriately, and the mould will inevitably be corrected after the trial moulding. As a result, the concave part will increase in size and the convex part will decrease in size.
Therefore, the shrinkage rate is set to a small value for the concave part size and a large value for the convex part size. For example, in injection moulding gears, gears can not mesh when the size of the outer diameter becomes large, and when it becomes small, only the gap becomes large, so the shrinkage rate should be set at a small value.
Special Precision Injection Moulding Design Guide 2. To prevent fluctuations in the shrinkage rate of moulding
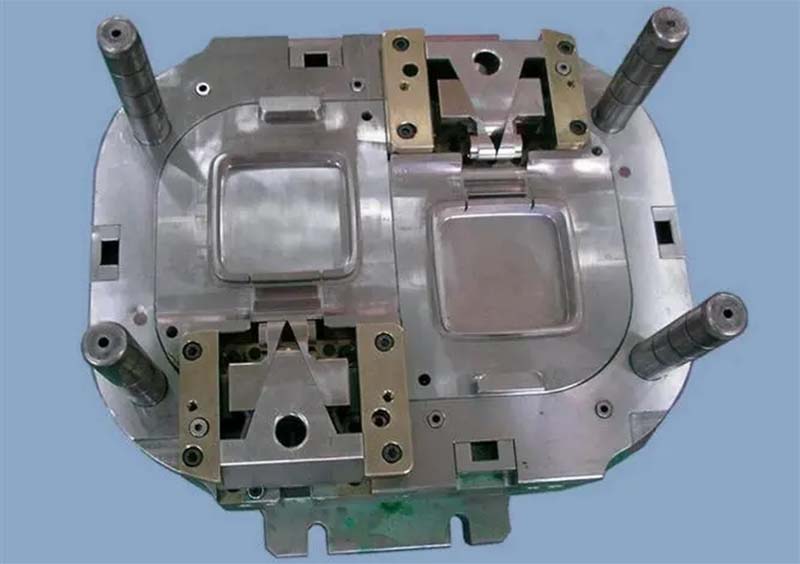
Precision injection moulding, must really can be made according to the size of the premise of the mould. However, even if the size of the mould is certain, the actual size of the product is also different due to the actual shrinkage. Therefore, in the process of precision injection moulding, the control of shrinkage is very important.
Shrinkage is related to the mould design but also varies depending on the resin batch, and if the pigment is changed, the shrinkage will also be different; due to the different moulding machines, the setting of the moulding conditions, the reproducibility, and the fluctuations in the action of each moulding cycle, which fluctuates the actual shrinkage rate, and so on, and thus, the control of shrinkage rate is difficult.
The mould size can be obtained by adding the shrinkage rate to the product size, so it is necessary to consider the shrinkage rate as a major factor when designing the mould. These effects vary depending on factors such as resin and moulding conditions.
The main factors affecting moulding shrinkage are the below factors.
1. Resin pressure
Resin pressure has a great influence on shrinkage. If the resin pressure is high, the shrinkage becomes small and the product size is large. Even in the same mould cavity, the resin pressure varies depending on the shape of the product, resulting in differences in shrinkage. In the case of multiple cavities, the resin pressure in each cavity is likely to vary, resulting in different shrinkage in each cavity.
2. Mould temperature
Whether it is a non-crystalline resin or a crystalline resin, if the mould temperature is high, the shrinkage rate will increase. Precision moulding requires that the mould temperature be maintained at a specific temperature. When designing the mould, attention must be paid to the design of the cooling circuit.
3. Gate Cross Section Area
Generally speaking, the shrinkage rate changes when the gate cross-section area is changed. Shrinkage decreases as the gate size increases, which is related to the fluidity of the resin.
4. Product Wall Thickness
The thickness of the product wall also affects the shrinkage rate.
For non-crystalline resin, because the resin on the wall thickness of the shrinkage tendency is different, wall thickness is large, shrinkage is also large; on the contrary, shrinkage becomes small.
In the case of crystalline resins, particularly large variations in wall thickness must be avoided. In the case of multiple cavities, if there is a difference in cavity wall thickness, the shrinkage rate will also be different.
5. Reinforcement content
When the resin is reinforced with glass fibers, the more glass fibers are added, the lower the shrinkage will be. Shrinkage in the flow direction is smaller than that in the transverse direction and varies greatly depending on the resin. To prevent twisting and warping, the shape, position, and number of sprues must be considered.
6. Orientation
Directionality varies greatly, but it exists for all resins. The orientation of crystalline resins is particularly large and varies depending on wall thickness and moulding conditions.
In addition, shrinkage after moulding occurs. The main factors affecting post-moulding shrinkage are internal stress, crystallization, temperature, and humidity.
Measures that can be taken as the below.
(1) Runner and gate balance
Shrinkage varies due to resin pressure. In the case of single-cavity moulds with multiple gates as well as in the case of multi-cavity moulds, gate balancing is required for the same mould filling. Resin flow is related to the flow resistance in the runner, so it is better to balance the runner before balancing the gate.
(2) Cavity arrangement
To make it easy to set the moulding conditions, it is necessary to pay attention to the arrangement of the mould cavities. Since the molten resin will be heated into the mould, the temperature distribution of the mould will be in the form of concentric circles centered on the gate under the general arrangement of the mould cavities.
Therefore, when selecting the arrangement of the mould cavities of a multi-cavity mould, it is necessary to obtain the balance of the runners easily and to take the concentric circle arrangement centered on the gate.
Special Precision Injection Moulding Design Guide 3. To prevent moulding deformation
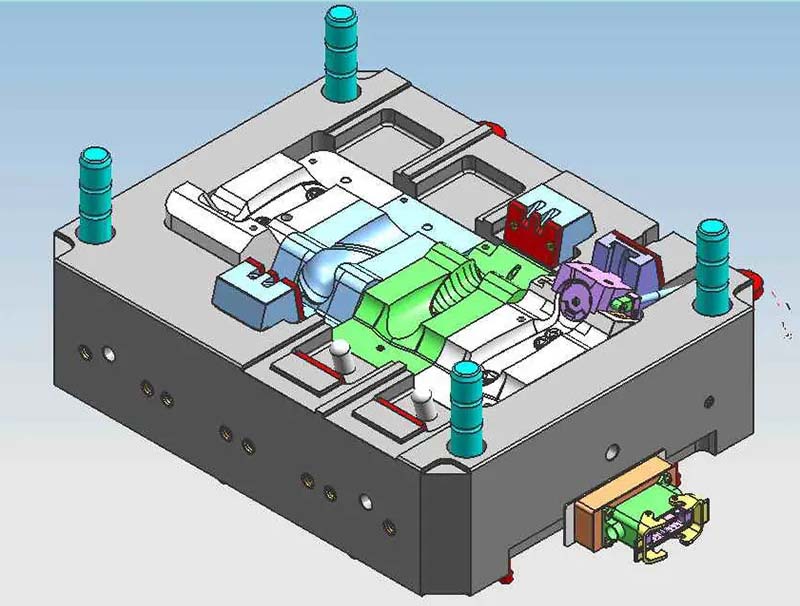
The reason for moulding deformation is that there is internal stress under uneven shrinkage, so it is necessary to prevent uneven shrinkage. In the case of round products with a hole in the center, it is necessary to have a gate in the center.
However, when there is a large difference in shrinkage between the resin flow direction and the vertical direction, the disadvantage of ellipticity occurs. Therefore, when a higher precision of roundness is required, a 3-point or 6-point gate is designed, but due attention is paid to the balance of each gate.
When using a side gate, a 3-point gate will increase the inner diameter of the cylindrical product. In the case that the exterior and end surfaces do not allow any trace of the gate, the use of the inner multi-point equalization gate can be used sparingly, and good results can be obtained.
Special Precision Injection Moulding Design Guide 4. Preventing deformation during demoulding
Precision products are generally smaller, thinner wall thickness, and some have many thin bars. Mould design must be considered so that products are not deformed, and can be properly demoulded.
For small shrinkage resin, when the moulding pressure is high, need to pay attention to products easy to stay in the mould cavity. For example, with small shrinkage resin moulding gear, the gear part of the mould cavity is best designed in the ejector side of the template;
In the use of the top bar, need to pay attention to the number of deformations of the top bar and the position of the top pressure; with holes in the gear need to be core pins, which will help to help in the ejector in the ejector parallel to the ejector, and need to be set in the ejector side of the template.
For angular products, a punching template can be used for ejection, and deformation can be prevented by using this template for ejection. General precision products of the pull-out slope are small, to reduce the release force, the need for mirror processing, grinding direction must be the direction of the pull-out, according to the direction of the pull-out of the design of easy to grind the chunks of the core.
Special Precision Injection Moulding Design Guide 5. Prevent the fluctuation of mould accuracy
To ensure the positioning of sliding parts in each cycle, it is necessary to prevent fluctuations in the accuracy of the mould. To maintain the accuracy of the sliding parts, the sliding parts should be quenched, ground and the sliding part of the side core should have a positioning part of the withdrawal.
Besides the 5 Special Precision Injection Moulding Design Guides article, you may also be interested in the below.
Stamping Die Design Guidelines, 75 Taboos And Rules
Mechanical Design Steps and 525 Taboos
6 Common Plastic Injection Molding Process Techniques
What is Multi-material Injection Molding?
How to Increase the Brightness of ABS Plastic Products?
Hot Runner Injection Molding Defects and Troubleshooting