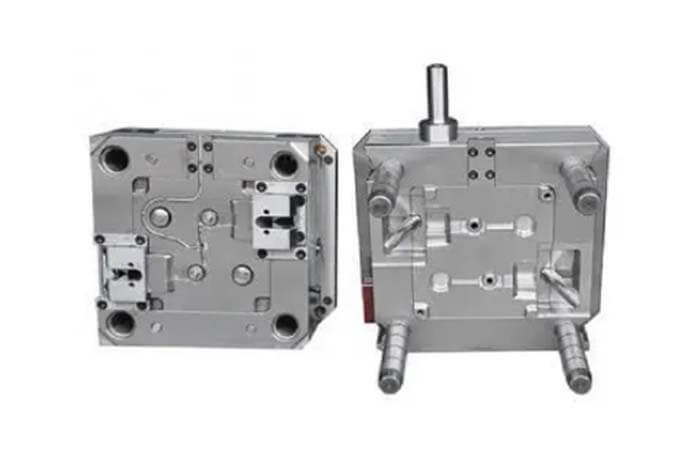
This article discusses the effect of mold temperature in injection molding in 4 areas:
What are the factors that affect the cooling of the injection mold?
What are the effects of the temperature of the injection mold on the injection molded parts?
How does mold temperature affect injection molding process?
What is the role of mold temperature on the quality control of injection molded parts?
First, mold temperature in injection molding effect injection molding process
How does mold temperature affect the injection molding process?
Mold temperature is the most important variable in injection molding. Regardless of the type of plastic, the temperature that forms the basic surface of the mold must be ensured. A hot mold surface keeps the plastic surface liquid for a long time, enough to create pressure in the cavity.
Mold temperature has a large impact on the performance and apparent quality of the molded part. The level of mold temperature depends on the characteristics of the plastic, the size and structure of the molded part, its performance and other process conditions.
The mold temperature for common plastic material:
Plastic Material | Mold Temperature(℃) |
ABS | 50-90 |
PP | 50-75 |
POM | >90 |
LDPE | 50-70 |
HDPE | 30-70 |
PVC-soft | 15-50 |
PVC-rigid | 30-50 |
PS | 10-40 |
PA6 | 70-120 |
PA66 | 70-120 |
PMMA | 50-70 |
TPR | 50-70 |
PC | 80-100 |
There are many ways to control the mold temperature, such as natural heat dissipation, water cooling, electric heating, etc. But no matter what method is used to set the mold temperature, it is cooling for the molten material because it needs to set the molded part and also facilitate the mold release.
The main purpose of controlling the mold temperature and the effect of mold temperature on the injection molded parts is to heat the mold to the working temperature and to keep the mold temperature constant at the working temperature. The cycle time can be optimized to ensure the stable quality of the injection molded part.
Mold temperature affects surface quality, flowability, shrinkage, molding cycle and deformation.
High or low mold temperatures can have different effects on different materials. For thermoplastics, higher mold temperatures will generally improve surface quality and flow, but will increase cooling time and cycle time.
A lower mold temperature will reduce shrinkage within the mold, but will increase shrinkage of the molded part after release. And for thermoset plastics, a higher mold temperature will usually reduce cycle time, and the time is determined by the time required for the part to cool. In addition, in the processing of plastics, a higher mold temperature will also reduce the plasticizing time and reduce the number of cycles.
For the molding of amorphous plastics, it does not undergo a phase transition after it is injected into the mold cavity and cured as the temperature decreases. The mold temperature mainly affects the mold filling speed. For plastics with high viscosity, such as PC, PSF, PI, PPO, etc., the mold temperature should be higher; while for amorphous plastics with low or medium viscosity, such as PS, CA, etc., the mold temperature should be lower.
For the molding of knotted plastics, the mold temperature plays a decisive role in the degree of knotting and knotting conditions. When the mold temperature is high, the cooling rate is small and the crystallization rate is large.
In addition, high mold temperature is also conducive to the relaxation of macromolecular bonds and reduce molecular orientation, it is mainly applicable to PET, PBT and other plastics. Such as polyolefins using high mold temperature will appear late crystallization, thus causing post-shrinkage of plastic parts and changes in performance, therefore, to use low mold temperature, its main plastic varieties are: PS, PVC, PE, PP, PA, etc.
Mold temperature control methods: Many molds, especially thermoplastics for engineering, operate at relatively high temperatures. If the mold is not insulated, the heat lost to the air and injection molding machine can easily be as much as that lost from the injection cylinder.
If possible, insulate the surface of the mold. If considering a hot runner mold, try to reduce the heat exchange between the hot runner section and the cooled injection molded part. This approach will reduce energy loss and warm-up time.
Second, mold temperature in injection molding effect mold cooling
What are the elements that affect the cooling of the injection mold?
There are many factors that affect the cooling of the precision injection mold, such as the shape of the plastic part and the design of the parting surface, the variety, temperature and flow rate of the cooling medium, the geometric parameters and spatial arrangement of the cooling pipe, the temperature of the melt, the ejection temperature and mold temperature required by the plastic part, the interaction of the heat cycle between the plastic part and the mold, etc.
Low precision injection mold temperature can reduce the molding shrinkage rate of plastic parts, average mold temperature, short cooling time, fast injection speed can reduce the warpage deformation of plastic parts, on crystalline polymers, progress in mold temperature can make the size of plastic parts stable, prevent post-crystallization phenomenon, but it will lead to longer molding cycle and plastic parts brittle defects.
As the crystallinity of crystalline polymers progresses, the stress cracking resistance of plastics decreases, so it is advantageous to reduce the temperature of precision injection molds. However, for amorphous polymers with high viscosity, the stress cracking resistance is directly related to the internal stress of the molded part, so it is beneficial to lower the precision injection mold temperature and mold filling speed to reduce the replenishment time.
Reducing the temperature of precision injection mold can improve the appearance quality of plastic parts. Mold temperature directly affects the plastic filling, molding, molding cycle and part quality, and the mold temperature depends on the plastic crystallinity, part size and structure, performance requirements and other process conditions such as melt temperature, injection speed, injection pressure and molding cycle.
Third, mold temperature in injection molding effect injection molded parts
What are the effects of injection mold temperature in injection molded parts?
- Low mold temperature can reduce the molding shrinkage of plastic parts.
- Uniform mold temperature, short cooling time and fast injection speed can reduce the warpage deformation of plastic parts.
- For crystalline polymers, increasing the mold temperature can make the size of the molded part stable and avoid post-crystallization, but it will lead to longer molding cycle and the defect of brittle molded parts.
- As the crystallinity of crystalline polymers increases, the stress cracking resistance of plastics decreases, so it is advantageous to reduce the mold temperature. However, for high viscosity amorphous polymer, since its stress cracking resistance is directly related to the internal stress of the plastic part, it is advantageous to increase the mold temperature and mold filling speed to reduce the replenishment time.
- Increasing the mold temperature can improve the surface quality of the plastic parts. Mold temperature is determined during the injection molding process, mold temperature directly affects the plastic filling, plastic part setting, molding cycle and plastic part quality.
- The temperature of the mold depends on the crystallinity of the plastic, the size and structure of the part, the performance requirements and other process conditions such as melt temperature, injection speed, injection pressure and molding cycle.
For amorphous polymers, the melt is injected into the mold cavity and cured as the temperature decreases, but no phase transformation occurs, and the mold temperature mainly affects the viscosity of the melt, i.e., the mold filling rate. Therefore, for amorphous plastics with low and medium melt viscosity, such as polystyrene and cellulose acetate, the cooling time can be shortened by using a lower mold temperature.
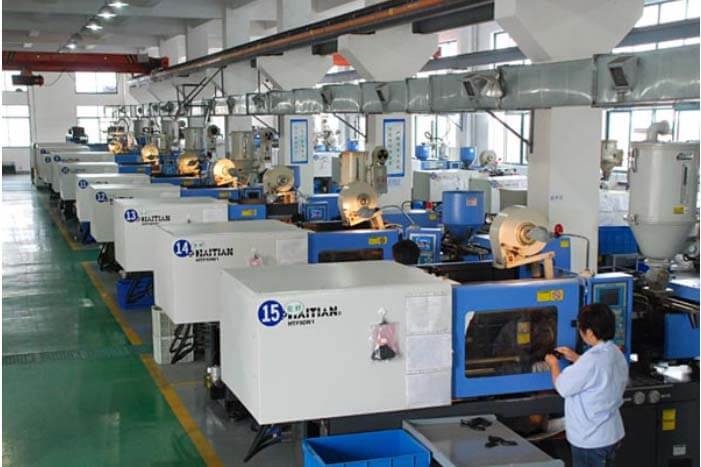
How to melt temperature impact molded products?
Depending on the type of resin used, there are several different ways in which the melt temperature may affect the final product being created. These ways include:
Viscosity of the resin:
The higher the melt temperature, the lower the viscosity. If the temperature is too high, your resin will be too thin to fill the mold properly, resulting in an incomplete product.
Molecular weight of the resin within the molded part:
The higher the melt temperature, the lower the weight. Using a higher weight resin means that more resin will be drawn into your final product, which means it is stronger and more durable.
Part shrinkage:
When you’re talking about injection-molded materials, “shrinkage” actually means expansion; drawing in too much material can result in a thick and brittle end product, while drawing in too little can leave you with a hollow part. If you plan to use a second resin to enhance the molding of an existing product, make sure its melt temperature is low; this will prevent damage or even an explosion due to excessive pressure in the mold cavity.
Fourth, mold temperature in injection molding effect injection molded parts quality control
What is the role of mold temperature on the quality control of injection molded parts?
Mold temperature refers to the surface temperature of the mold cavity in contact with the product during the injection molding process. Because it directly affects the cooling rate of the products in the mold cavity, thus it has a great influence on the inner performance and appearance quality of the products.
The influence of mold temperature on product appearance
Higher temperature can improve the fluidity of resin, which usually makes the surface of the parts smooth and shiny, especially to improve the surface aesthetics of glass fiber reinforced resin parts. It also improves the strength and appearance of the fusion line.
As for the etched surface, if the mold temperature is low, it is difficult to fill the melt to the root of the texture, which makes the surface of the product appear shiny and “transfer” the real texture of the mold surface, and after increasing the mold temperature and material temperature, the surface of the product can get the ideal etching effect.
Influence on the internal stress of the product
The formation of internal stress is basically due to the different heat shrinkage rate during cooling, when the product is formed, its cooling is gradually extended from the surface to the interior, the surface first shrinks and hardens, and then gradually to the interior, in the process due to the difference between the speed of shrinkage and internal stress.
When the residual internal stress in the plastic part is higher than the elastic limit of the resin, or under the erosion of certain chemical environment, the surface of the plastic part will be cracked. Studies on PC and PMMA transparent resins show that the residual internal stresses are compressive in the surface layer and tensile in the inner layer.
The surface compressive stress depends on the cooling condition of the surface. A cold mold causes the molten resin to cool down rapidly, resulting in a high residual internal stress in the molded part. The mold temperature is the most basic condition to control the internal stress, and a slight change of mold temperature will have a great change on its residual internal stress.
Generally speaking, each product and resin has its own minimum mold temperature limit for acceptable internal stress. When molding thin wall or long flow distance, the mold temperature should be higher than the minimum limit in general molding.
Improve product warpage
If the cooling system of the mold is not designed properly or the mold temperature is not controlled properly, insufficient cooling of the plastic part will cause warpage of the plastic part.
For mold temperature control, the temperature difference between Yang mold and Yin mold, mold core and mold wall, mold wall and insert should be determined according to the structural characteristics of the product, so as to use the different cooling and shrinkage speed of each part of the control mold, the plastic part tends to bend to the higher temperature side of the traction direction after demolding, to offset the orientation shrinkage difference and avoid warping and deformation of the plastic part according to the orientation law.
For the shape and structure of completely symmetrical plastic parts, the mold temperature should be maintained accordingly, so that the cooling of each part of the plastic part is balanced.
Affect the molding shrinkage of the product
Low mold temperature makes the molecules “freeze orientation” faster, making the melt in the cavity of the freezing layer thickness increases, while the low mold temperature hinders the growth of crystallization, thus reducing the molding shrinkage of the product.
On the contrary, if the mold temperature is high, the melt cools slowly, the relaxation time is long, the orientation level is low, and at the same time, it is conducive to crystallization, and the actual shrinkage rate of the product is larger.
Influence the heat deflection temperature of the product
Especially for crystalline plastics, if the product is molded at a lower mold temperature, the molecular orientation and crystallization are instantly frozen, and when a higher temperature is used or under secondary processing conditions, the molecular chains will partially rearrange and crystallize the process, making the product deform at even much lower than the heat deflection temperature (HDT) of the material.
The correct approach is to use the recommended mold temperature close to its crystallization temperature, so that the product can be fully crystallized during the injection molding stage and avoid such post-crystallization and post-shrinkage in high temperature environment.
In conclusion, mold temperature is one of the most basic control parameters in the injection molding process, and is also a primary consideration in mold design. Its influence on the molding, secondary processing and end-use process of the product cannot be underestimated.
Besides the What Are The 4 Effects of Mold Temperature In Injection Molding article, you may also be interested in the below.
Stamping Die Design Guidelines, 75 Taboos And Rules
Mechanical Design Steps and 525 Taboos
6 Common Plastic Injection Molding Process Techniques
What is Multi-material Injection Molding?
How to Increase the Brightness of ABS Plastic Products?
Hot Runner Injection Molding Defects and Troubleshooting